Design Rule Setup
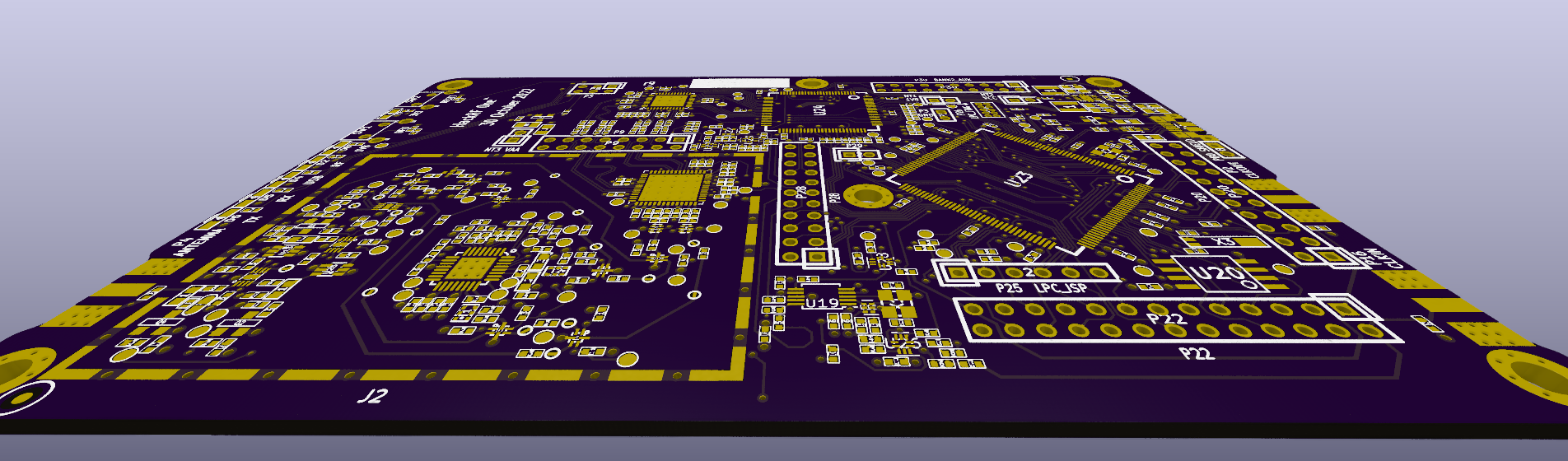
The design rules describe manufacturing constraints, and help Kicad ensure that the design you create can be manufactured correctly.
Design Rules Editor
The manufactuing config dialogue box is found under File
> Board Setup
.
Most values provided below have conversions, but Kicad will automatically convert to your preferred units if you enter a unit indicator. EG, entering 0.01in
, 0.254mm
, or 10 mil
will provide the same end result.
Board Stackup > Physical Layers
This page lets you indicate the PCB layer count, and physical properties of the PCB.
Copper Layers
should be set to 2
, 4
, or 6
. Using other layer counts will often result in issues in exporting files for production.
All other values: These depend on which service you need for production, and provided here: OSH Park Services. Entering these values is only required if your design will use Kicad’s DRC/DRU tools to calculate controlled impedance. During production, we will disregard user-provided values, and use the stackup indicated for the selected service.
Board Stackup > Soldermask/Paste
Solder Mask Expansion
should usually be set to 2mil (0.0508mm), which pairs well with our production tolerances. This can be decreased as needed, but increasing this value is not recommended. For additional information, see Understanding Stop Mask Expansion.
Solder Mask Expansion Web Width
should usually be set to 0
.
Tent Vias
is optional, but typically recommended. When checked, vias will be inaccessible for soldering; When unchecked, they will be exposed. Vias and through holes used for components will always be exposed as indicated in their footprint.
Solder Paste
options will vary, and depend on your assembler or stencil manufacturer.
Design Rules > Constraints
These vary slightly based on production service.
Setting | 2 Layer Services | 4 Layer | 6 Layer |
---|---|---|---|
Minimum Clearance | 6mil (0.1524mm) | 5mil (0.127mm) | 5mil (0.127mm) |
Minimum track Width | 6mil (0.1524mm) | 5mil (0.127mm) | 5mil (0.127mm) |
Minimum Connection Width | 6mil (0.1524mm) | 5mil (0.127mm) | 5mil (0.127mm) |
Minimum Annular Ring | 5mil (0.127mm) | 4mil (0.1016mm) | 4mil (0.1016mm) |
Minimum Via Diameter | 20mil (0.508mm) | 18mil (0.4572mm) | 16mil (0.4064mm) |
Copper to hole clearance | 5mil (0.127mm) | 5mil (0.127mm) | 5mil (0.127mm) |
Minimum Through Hole | 10mil (0.254mm) | 10mil (0.254mm) | 8mil (0.2032mm) |
Hole to hole clearance | 5mil (0.127mm) | 5mil (0.127mm) | 5mil (0.127mm) |
Minimum uVia diameter | 20mil (0.508 mm) | 18mil (0.4572 mm) | 16mil (0.4064 mm) |
minimum uVia Hole | 10mil (0.254mm) | 10mil (0.254mm) | 8mil (0.2032mm) |
Silkscreen Min Item Clearance | user preference | ||
Silkscreen Min Text Height | user preference | ||
Silkscreen Min Text Thickness | 5 mil (0.127mm) | 5 mil (0.127mm) | 5 mil (0.127mm) |
Design Rules > Net Classes
These can be configured to user preferences, and allow customized DRC depending on the type of signal you’re routing.
The “Default” net class will use the minimum DRC values.